In the past, face masks and respirators (MAR) have been largely manufactured with single-use plastic materials. This has resulted in an increased waste burden from these disposable products, and further environmental concerns regarding disposal of MARs after use.
Various filtration technologies have been explored to enhance the performance and sustainability of MAR, including nanotechnology, membrane technology, and composite and impregnated media structures. Moreover, the use of cellulose has become a promising option for producing biodegradable masks from local resources in response to the high demand resulting from the COVID-19 pandemic .
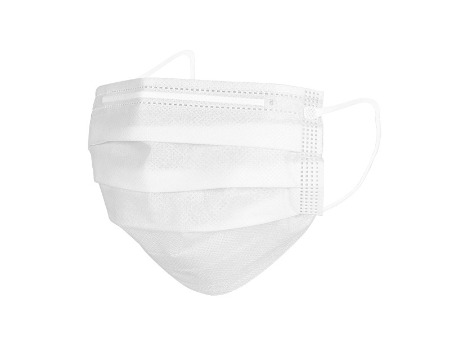
Nanotechnology/Meltblown Filter Layer
The antimicrobial filter of a nanomask is typically made from a cellulose and polymer/polyester layer containing positively charged Cu/Zn ions or polyhexamethylene biguanide hydrochloride, which attracts and disrupts negatively charged membranes of microorganisms and thus provides protection against airborne pathogens and other contaminants. Its advantages include high filtration efficiency, lightness, water-resistant characteristics, and long service life.
Non-Woven Filter Layers
The nonwoven fabric of a mask should be made from multiple layers of different fabrics, such as cotton and linen, polyester or nylon, and their blends. The fabrics should be selected for their permeability and resistance to aerosol and water droplets, as well as their softness and comfort.
Metal-Based Antimicrobial Technologies
There are many companies that offer metal-based antimicrobial technologies, primarily Ag, which have non-toxicity, eco-friendliness, and high thermal stability.